The Importance Of Molds For Rotomolding
- justinsmith6845
- Jan 11, 2022
- 2 min read
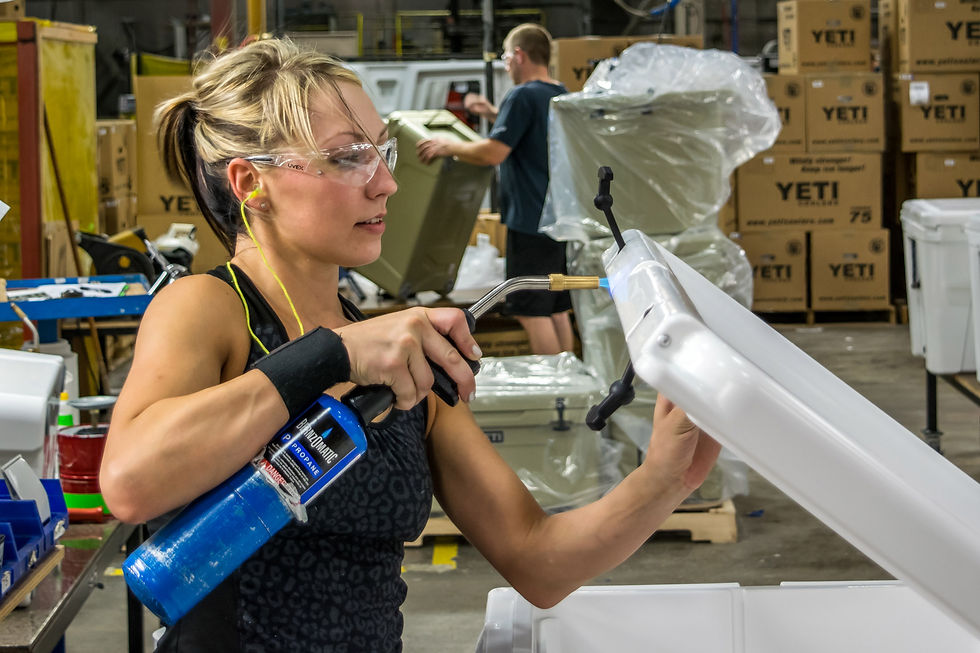
Molds for Rotomolding are an essential part of any product manufacturing process. During this process, a mold is a tool that will be used to create plastic parts. The tooling is made of soft metal, which is why it is easy to repair or replace. Most of the resin that is used is polyethylene, which is a low-degradation plastic that is resistant to high heat. The molds will typically include ribs, kiss-offs, and inserts. If the mold is complex, foam reinforcement will also be included in the product. Grangerplastics is here which will help you to make a right decision for you.
Rotomolded products are also more durable. Because they are molded to fit together, rotomolded products can withstand a variety of harsh environments. A popular example of this type of product is the Granger ISS Tornado Shelter door. The ISS door meets or exceeds FEMA 320, 361, and ICC 500 debris impact standards. Its rotomolded construction can withstand a 15-pound 2x4 that hits it at 100 miles per hour.
The raw materials used for rotational molding vary widely in physical properties and intended use. These raw materials may contain additives or colors. Therefore, choosing the right raw material for your product is critical for its success. Proper design of the mold will help your project run as smoothly and efficiently as possible. For instance, the aethetics of the final product must be taken into consideration in the design phase. These factors are key to ensuring that your product is as good as possible.
The process of rotomolding requires a number of steps. A rig is necessary to get the right result, and there are a lot of variables that can affect that. The process requires careful planning and careful analysis of the design. With the right design, the mold will produce the desired result. So, it's worth investing in a mold that will make your next project a success!
While a rotomolding mold should be durable and easy to clean, it should not be too complex. Various factors must be considered, including the size of the mold, and the material. It should not be too large and should be durable enough to stand up to the process. It should be easy to rotate. It should have a high temperature-resistance. It should be insulated so that it doesn't deform the product.
The parting surface is another crucial feature to consider. The parting surface is where raw materials will be inserted into the mold. It should be as smooth and non-abrasive as possible, so that it can be easily handled. It should also be designed so that the internal pipe and metal threads are visible. The quality of the parting surface is essential. With the right mold, you can produce your product in a short time.
Commentaires